Well, no sealing wax: just sealing thin CyA.
The large tube (S-IC, Interstage, S-II) is done, except for touch-up, masking, and painting. It's on to the S-IVB now. First step is to build the transition between the S-II and the S-IVB (big tube and third stage). This requires building a centering ring-couple set between the small S-IVB tube and the large tube that comprises the S-IC and S-II.
Ideally, this is pretty easy: two centering rings, and a coupler constructed earlier (one of the first steps) by slightly sectioning a small piece of tube that's the same size as the large tube so that it just fits inside the large tube. I made this coupler just a little too big, so out came the sanding block and, since I took off all the outer layers (the ones that coat the cardboard fibers to keep them from fraying), the thin CyA to reseal the coupler. Then, more sanding, since the thin CyA causes the outer fibers of the cardboard to swell, and the surface gets rough.
Just about done, though. Then, it's on to attaching the wrap that gives me the most cause for concern: the third stage wrap, that overlays the transition's taper.
Saturday, February 28, 2009
Thursday, February 26, 2009
Specialized Techniques, Ullage Rocket Scars
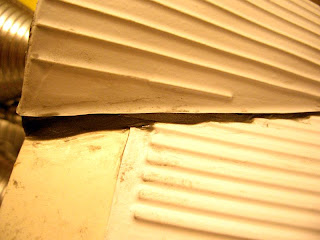
Building the Apogee Saturn V requires all these specialized techniques that I've not used before. Letting CyA wick to seal the edges of the thin plastic wraps, feathering epoxy clay to smooth over joints that don't meet quite perfectly, and who-knows what else in the offing.
I had to come up with one of my own (the two above are in the instructional videos that come with the kit): drizzle a little canopy cement and let it wick—sometimes help it wick—under an edge of a plastic wrap. I used this technique to seal the edges of the scars from the ullage rockets that I removed in order to model Apollo 15 more closely.
The frustrating part is that just about when I get comfortable and competent with one of these techniques, I'm done using it on the rocket!
Fin Fairing Wraps, and Manufacturing Tolerances
Finally: the fin fairing wraps are attached! Unfortunately, some of the manufacturing tolerances are a bit loose. None of the wraps seemed to extend quite as far as I'd expected. It's just a bit of extra craftsmanship to get things looking reasonably good, but it would be nice if the parts were made to better tolerances. (The same issue applies to some of the large tube wraps: they're too short!)
Saturday, February 21, 2009
STB-1
I'm working to determine the limits of indirect staging (sometimes known as gap staging): how far apart can the booster and sustainer motors be, and still get reasonably reliable ignition? I built STB-1 (Staging Test Bed #1), pushing the first stage out to about 40 cm, staging an Estes D12 to a B4. The first flight worked perfectly, though there was some interesting tip-off shortly after launch and an odd sort of corkscrew in the flight path.
The second flight wasn't nearly as successful: the sustainer failed to light.
The booster motor mount tube has four vent holes, roughly 3mm diameter, about 4cm or so from the top. These vent into the airframe, with vent holes drilled into the middle and after centering rings (BT-60 airframe). I'd thought that, perhaps, the failure's cause was clogged vent holes in the middle centering ring. Post-flight dissection showed that not to be the case.
The sustainer's motor mount had been dislodged and shoved well forward in the airframe. I couldn't tell if this happened on impact or during staging—I would guess on impact, though. There was a small hole in the forward centering ring, though, to provide clearance for the sustainer's engine retaining hook; after the second flight, it looked to me as though that hole had grown. It's possible that the stages are too far apart for reliable ignition, and it's possible that the hole in the forward centering ring allowed enough pressure to vent forward that the stages separted before sustainer ignition. (That forward centering ring is too far forward: it should not be impinging on the sustainer's engine hook.)
Perhaps more testing to come.
The second flight wasn't nearly as successful: the sustainer failed to light.
The booster motor mount tube has four vent holes, roughly 3mm diameter, about 4cm or so from the top. These vent into the airframe, with vent holes drilled into the middle and after centering rings (BT-60 airframe). I'd thought that, perhaps, the failure's cause was clogged vent holes in the middle centering ring. Post-flight dissection showed that not to be the case.
The sustainer's motor mount had been dislodged and shoved well forward in the airframe. I couldn't tell if this happened on impact or during staging—I would guess on impact, though. There was a small hole in the forward centering ring, though, to provide clearance for the sustainer's engine retaining hook; after the second flight, it looked to me as though that hole had grown. It's possible that the stages are too far apart for reliable ignition, and it's possible that the hole in the forward centering ring allowed enough pressure to vent forward that the stages separted before sustainer ignition. (That forward centering ring is too far forward: it should not be impinging on the sustainer's engine hook.)
Perhaps more testing to come.
Monday, February 16, 2009
Peeling Warps
After all that work to get the wraps down well, it's time to peel up a few small sections. Some of them are at the gaps between edges of a wrap, and in some of these I didn't go nuts trying to get those edges down, knowing that a tunnel cover would run over that. But, in some cases, it seems that the CyA wicked much further under the wrap than I'd have liked, especially at the forward end of the first stage tunnel cover.
It's painful.
It would have helped, I think, if we'd had some written instructions to browse: it's very difficult to browse quickly through the video instructions. A few more specific hints in the sections on attaching the wraps (e.g., "avoid getting glue under this-and-such part of that-and-such wrap, because you might want to remove that part of the wrap when attaching the tunnel covers") would really have helped, I think.
It's painful.
It would have helped, I think, if we'd had some written instructions to browse: it's very difficult to browse quickly through the video instructions. A few more specific hints in the sections on attaching the wraps (e.g., "avoid getting glue under this-and-such part of that-and-such wrap, because you might want to remove that part of the wrap when attaching the tunnel covers") would really have helped, I think.
Sunday, February 8, 2009
Time for Tunnels
Time, finally, to get the tunnel covers shaped, smoothed, primed, and glued. And the launch lugs. And, and, and. I'm glad to be back working with something other than those wraps!
Subscribe to:
Posts (Atom)